2022 ushered in an exciting and motivating year for the 3D printing industry. Innovations in print materials and print technologies have continued to move additive manufacturing into a major asset in the shift to industry 4.0. Here at PostProcess, we were bustling with renewed energy and enthusiasm about new solutions, technologies, partnerships, and team members. As always, our team was hard at work to continue to create innovative new solutions for post-processing. Here’s a look at a few of the significant events that happened here at PostProcess in 2022.
New FDM Support Removal Solution Now Available: The VORSA 500
In February, we announced our latest FDM Support Removal Solution: The VORSA 500™. The new VORSA 500 leverages our proven Volumetric Velocity Dispersion (VVD) technology to remove consistent, hands-free support structure removal on 3D-printed FDM parts. Joining our other FDM support removal solutions, the VORSA 500 provides the fastest cycle times in the industry, reducing support removal processing times by over 50% compared to submersible tank systems.
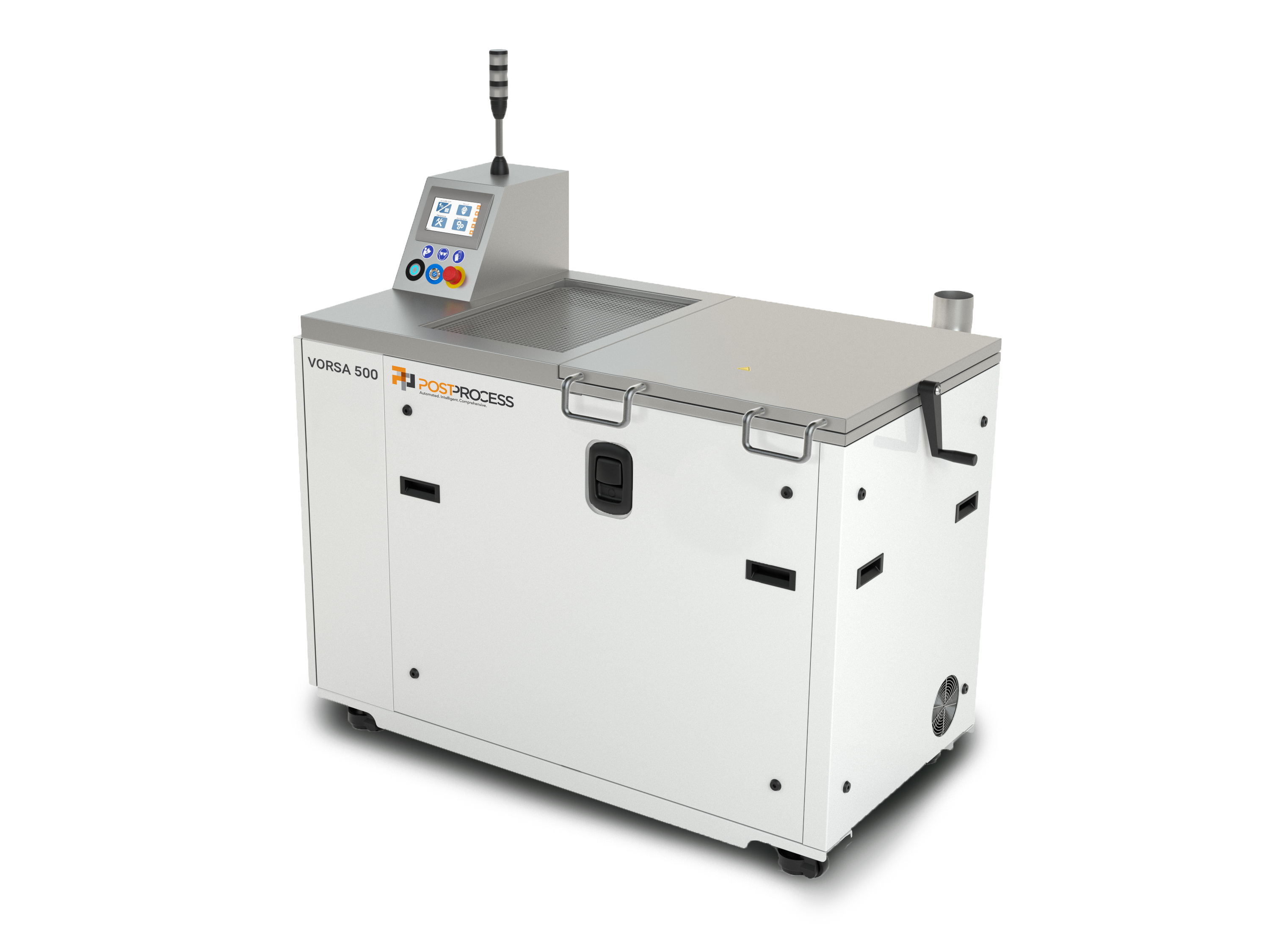
Enabled by our AUTOMAT3D® software platform, the VORSA 500 uses multi-dimensional spray coverage to ensure fast cycle times without damaging parts. It allows for quick dry times while maintaining part integrity because it does not saturate parts with detergent, thanks to the proprietary spray nozzle technology. With user-friendly software controls, operators have control over key process parameters and the ability to optimize cycles to produce consistent end parts.
“… the VORSA 500 demonstrates our continued market leadership in the additive manufacturing post-print space and provides the industry with the fastest FDM support removal solutions,” commented Rich Caplow, PostProcess Vice President, Product.
Automated Wax Support Removal Solution Announced
In May of this year, we announced our proprietary formulation: PLM-601-SUB. We developed this detergent to solve wax support removal concerns. Large batches of wax 3D-printed parts can be processed in our DEMI family of solutions with software-controlled parameters, making the process safe and easy for operators.
Thanks to its ability to make highly detailed patterns, 3D-printed wax casting is widely adopted across many industries and is especially useful for luxury and jewelry makers. While wax allows for highly detailed prints, it also creates incredibly fragile parts, making traditional post-processing methods difficult. Highly trained technicians are required, which forces overall low productivity.
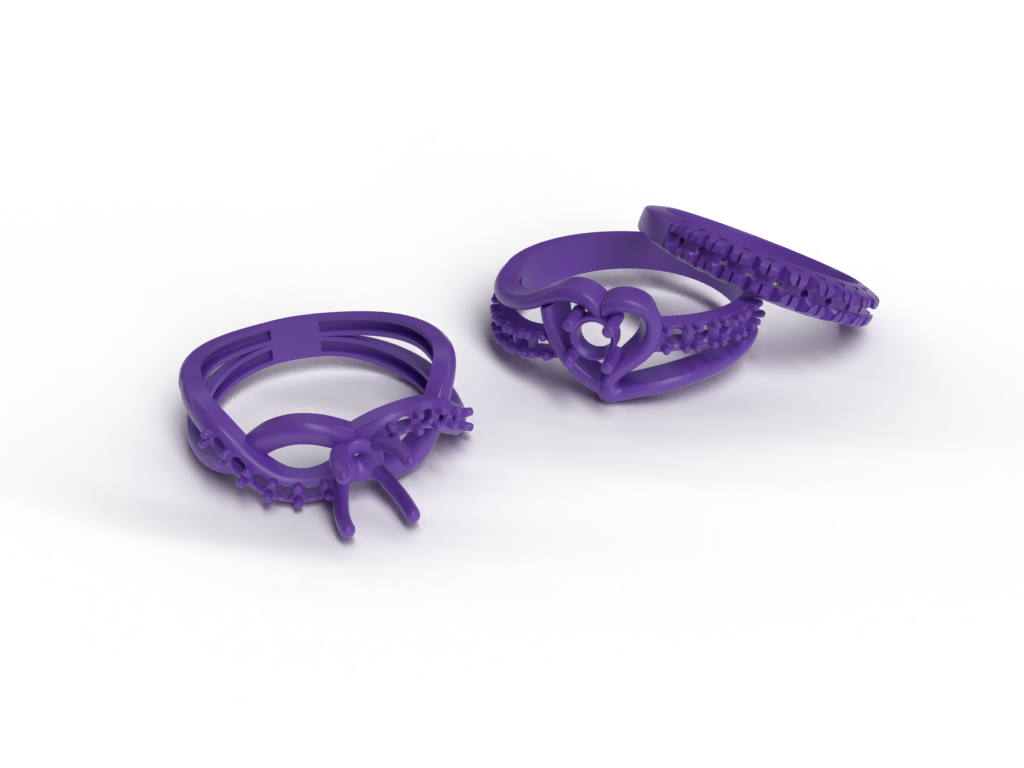
Traditional wax support removal also requires processing with IPA, which is typically time intensive with a multi-step process, inconsistent, and requires extensive manual labor with high technician attendance time. Safety concerns are associated with this form of support removal because of the necessity of heating the highly flammable IPA bath. The low longevity of IPA also hurts the environment due to the large amounts of waste generated.
“Effective wax support removal is a well-known obstacle for the industry. We are pleased to solve this post-processing challenge with a comprehensive solution that includes our newest industry-unique detergent,” stated Matthew Noble, Lead Chemist from PostProcess.
New Chief Marketing Officer Melissa Hanson Joins PostProcess Team
Industry and marketing veteran Melissa Hanson joined the PostProcess team in August as our Chief Marketing Officer (CMO). Hanson is a seasoned executive with deep expertise in spearheading disruptive innovation and leading high-performing teams to deliver exceptional value and transformational growth in the manufacturing and technology sectors. Hanson brings 17+ years of experience, which includes 8 years as a senior marketing leader in the additive manufacturing industry.
Said Hanson, “I am excited to join the talented and passionate team at PostProcess, and eager to lead the way in educating on its vision and mission because I believe it is one of tremendous impact.”
EOS Strategic Partnership Announced
October was an important month for us here at PostProcess. We announced our distribution partnership with EOS, a leading supplier of responsible manufacturing solutions via industrial 3D printing technology. Our VAD technology solution will allow us to provide a fully automated and sustainable depowdering solution for EOS customers.
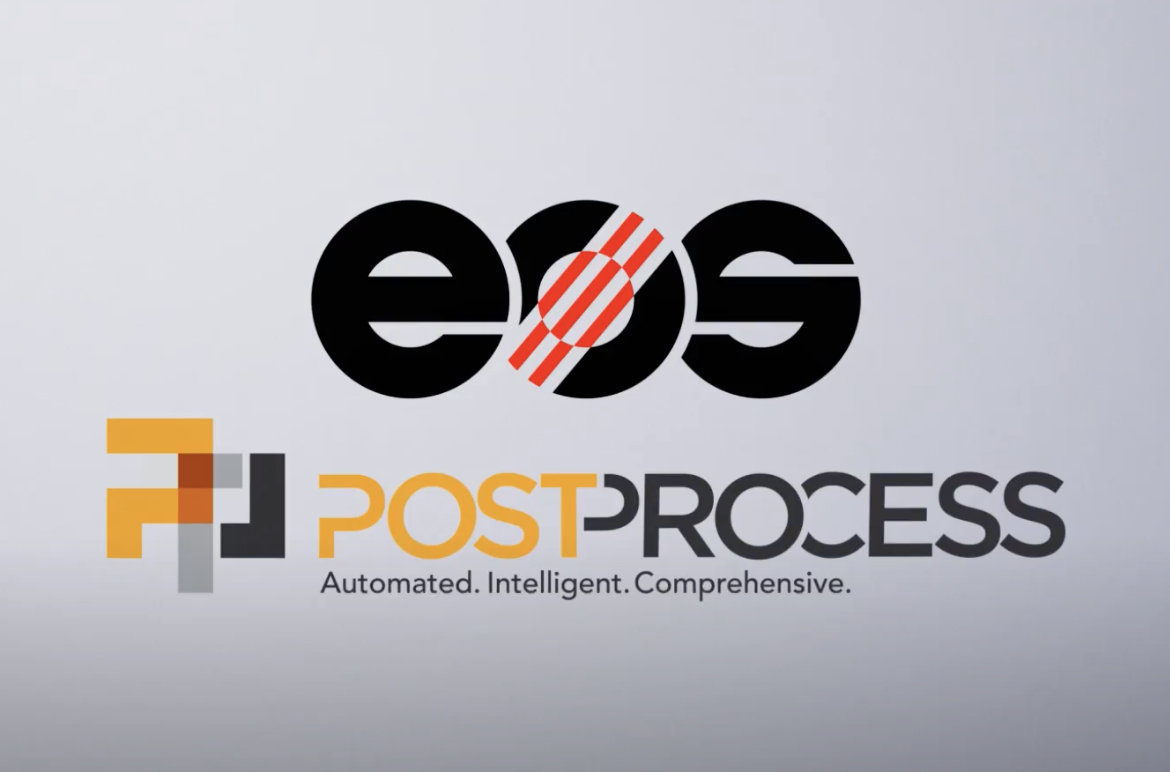
Variable Acoustic Displacement™, also known as VAD technology for short, automates gross depowdering for 3D printed parts. Current powder removal methods are highly manual or semi-automated and may cause safety and sustainability issues. Our VAD solution is thermodynamically controlled with video and infrared monitoring while releasing, transferring, and recovering loose powder particles hands-free, to mitigate these concerns.
Our patent-pending VAD technology uses software intelligence to optimize mechanical energy and closed-loop thermal and displacement techniques for revolutionary bulk depowdering results, enabling full process chain automation. The powder removal and recovery achieved with VAD technology improve process performance and control, providing customers with enhanced sustainability and employee safety, repeatability and productivity, and lower operating costs. Customers can print highly detailed and complex parts without worrying about breakage in the post-processing step.
“We are proud to solidify this partnership with EOS, a global leader in industrial 3D printing, to help end users more easily adopt the complete workflow of additive manufacturing and scale their operations,” stated Jeff Mize, PostProcess CEO.
4th Annual Post-Processing Survey Results Released
The Fourth Annual Post-Processing Industry Trends Survey was released on December 7th. This survey explores the post-processing needs and solutions by market and provides an in-depth, segmented look at additive post-processing across a myriad of applications. Our goal in surveying the market and assembling this data is to help make clear the path toward a successful future for Additive Manufacturing (AM) by recognizing the downfalls, considerations, and opportunities for all aspects of post-processing.
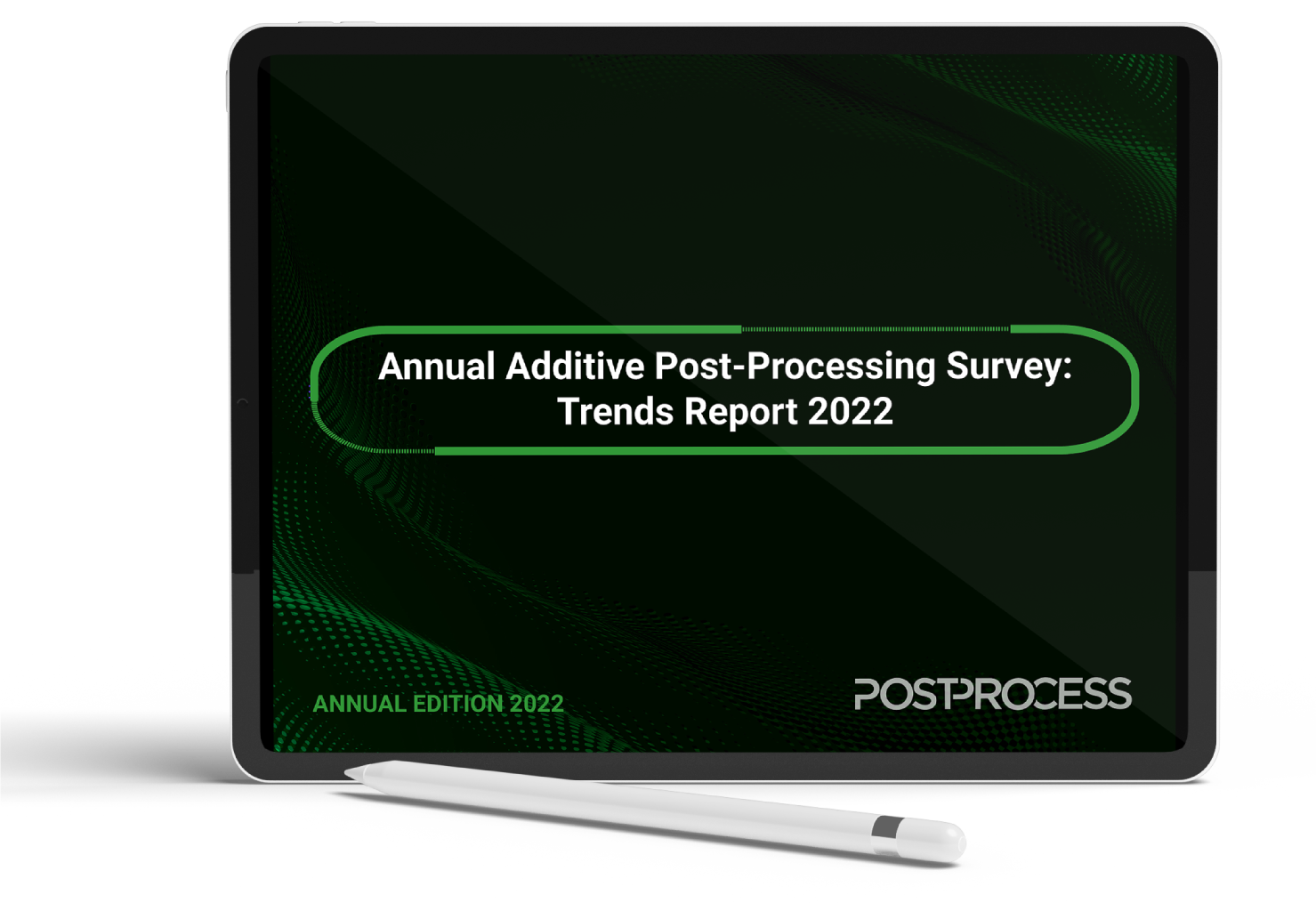
Within the report, learn more about 3D print technology trends, post-processing method trends, production vs. prototyping trends, post-processing expenditures, post-processing pain points, and post-processing investments.
This survey is the first and only of its kind to evaluate post-processing needs across the additive landscape, and is now available for download here: https://www.postprocess.com/trends-report/
2022 was a year of innovation and forward movement here at PostProcess. And while the year is wrapping up, we have so many exciting things coming up for 2023. We can’t wait to share all the exciting things we have in store for the new year, so stay tuned.
-> Want to connect? Contact Us
-> Return to Blog Homepage